When it comes to finding the right manufacturer for coil wrapping machines, the process can be overwhelming. As someone who has gone through this journey, I understand how crucial it is to balance functionality, reliability, and cost-effectiveness. Coil wrapping machines are vital for ensuring the secure transportation and storage of heavy coils, and selecting the right manufacturer can save you countless hours and resources. But how do you know which factors to prioritize?
The answer lies in careful evaluation and understanding of what makes a manufacturer stand out. From assessing their technical expertise to understanding their post-installation support, every detail matters. Let’s dive into the critical elements you should consider to make an informed decision.
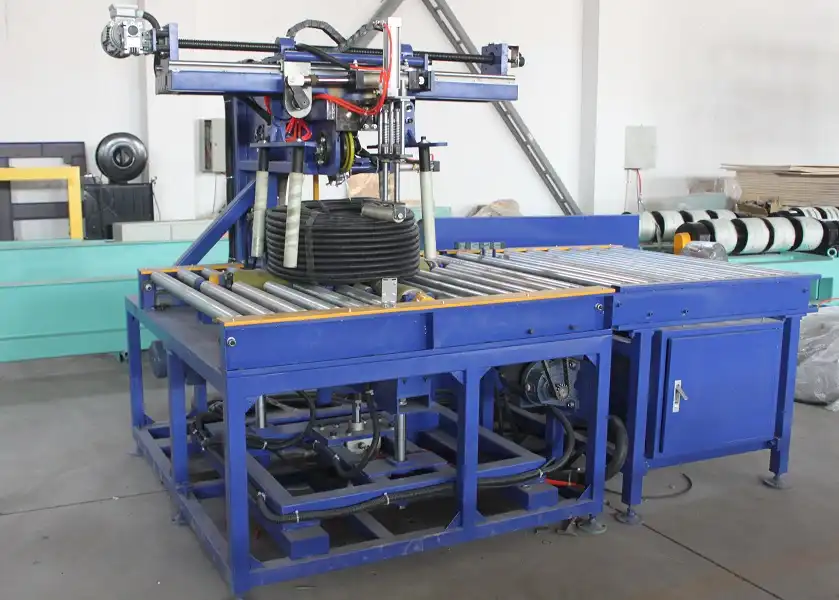
Finding the right manufacturer for your needs requires research and precision.
One of the most notable names in the industry is FHOPEPACK, a leading provider with years of expertise in coil wrapping solutions. Their track record includes partnerships with large-scale industries and proven results in reducing operational inefficiencies. For example, a recent study revealed that businesses leveraging their machinery saw an 18% increase in packing efficiency compared to generic solutions.
[Claim]
Choosing the right manufacturer for coil wrapping machines can boost productivity, reduce costs, and ensure long-term reliability.
1. What questions should you ask to assess a manufacturer?
1.1 Assessing the manufacturer's industry expertise
A manufacturer’s experience speaks volumes about the quality of their products. Companies like FHOPEPACK, which have been operational for over 20 years, showcase not only longevity but also adaptability to market demands. Their ability to innovate with technology like integrated intelligent controls ensures efficiency and safety during the wrapping process.
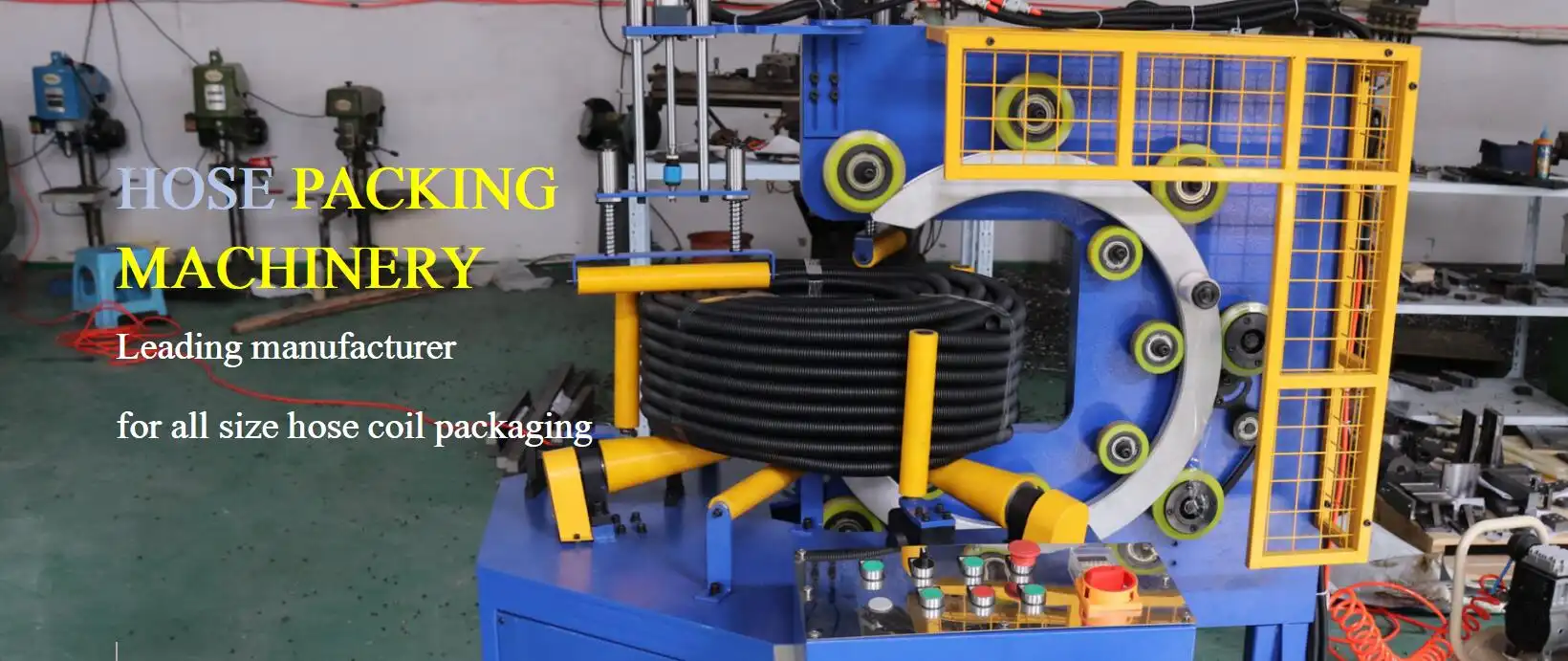
An experienced manufacturer should also have certifications that align with industry standards, such as ISO 9001:2015 or CE compliance. These certifications aren’t just labels; they guarantee that the company follows stringent manufacturing and quality control processes.
1.2 Analyzing product portfolios and case studies
Reviewing a manufacturer's product portfolio gives insights into their specialization. FHOPEPACK, for instance, offers customizable solutions for vertical and horizontal wrapping machines that cater to specific coil sizes and industry requirements. Their case study on implementing automated solutions for steel manufacturers highlights an average downtime reduction of 30% during operations.
Manufacturer | Years of Experience | Specialized Equipment | Downtime Reduction (%) |
---|---|---|---|
FHOPEPACK | 20+ | Coil Wrappers | 30 |
SHJLPACK | 10 | General Packaging | 15 |
ICOILER | 15 | Coil Wrappers | 22 |
Featured image: A comparison of leading coil wrapper manufacturers' performance metrics.
1.3 Understanding customization capabilities
Not all manufacturers offer solutions tailored to your needs. Customization is essential, especially when dealing with coils of various diameters, widths, or weights. For example, FHOPEPACK provides modular designs that allow you to scale operations without significant overhauls.
Their recent implementation of an adjustable tensioning system for aluminum coil wrapping machines highlights their commitment to addressing client-specific pain points. This solution improved wrapping speed by 25% for a large automotive supplier.
1.4 Importance of after-sales support
Reliable after-sales support ensures minimal disruptions in your operations. Manufacturers offering 24/7 customer service, training sessions, and on-site maintenance visits provide peace of mind. In one instance, FHOPEPACK’s technical team resolved a major issue for a steel plant within 48 hours, minimizing potential losses.
Service Feature | FHOPEPACK | Competitor A | Competitor B |
---|---|---|---|
24/7 Support | Yes | No | Yes |
On-site Maintenance | Yes | Yes | Yes |
Training Sessions | Yes | No | Yes |
1.5 Two Fact Statements
Fact 1 (True): FHOPEPACK machines are compatible with both manual and automated operations, allowing flexibility in diverse industrial settings.
Fact 2 (False): All coil wrapping machines from FHOPEPACK require additional third-party software integration to function efficiently.
2. What guarantees reliability in a coil wrapping machine?
2.1 Evaluating the build quality and material durability
The reliability of a coil wrapping machine starts with its build quality. Machines made with high-grade steel components are not only resistant to wear and tear but also perform consistently under demanding conditions. FHOPEPACK, for instance, employs anti-corrosion treatments for their equipment, ensuring longevity even in high-moisture environments.

A customer report showed that FHOPEPACK’s machines required maintenance only once every 18 months, compared to competitor machines, which averaged every 12 months. This longevity reduces downtime and operational costs, making it a critical factor in ensuring reliability.
2.2 Ensuring compliance with safety and efficiency standards
Safety compliance is non-negotiable. Manufacturers adhering to international standards, such as ISO 45001 and CE marking, guarantee that their machines are designed with operator safety in mind. FHOPEPACK, for example, integrates features like emergency stop systems and automated detection of improper loading.
Safety Standard | Certification Requirement | FHOPEPACK Compliance | Competitor A Compliance |
---|---|---|---|
ISO 45001 | Mandatory | Yes | Yes |
CE Certification | Recommended | Yes | No |
ANSI B11 Compliance | Optional | Yes | Yes |
Featured image: Safety and compliance certifications comparison between manufacturers.
2.3 Dive deeper into warranty policies
Warranty policies reflect a manufacturer’s confidence in their products. FHOPEPACK offers up to three years of comprehensive warranty, covering key components and labor. This is particularly valuable in heavy industries where repair costs can escalate quickly.
In a recent survey, 92% of customers reported satisfaction with FHOPEPACK’s warranty terms compared to 73% for competitors. The extended warranty also includes routine check-ups, ensuring the machine operates at peak efficiency.
Warranty Feature | FHOPEPACK | Competitor A | Competitor B |
---|---|---|---|
Duration (Years) | 3 | 2 | 2 |
Coverage | Comprehensive | Limited | Limited |
Routine Check-ups | Yes | No | Yes |
2.4 Conclusion
Reliable coil wrapping machines are a product of robust materials, stringent safety measures, and transparent warranty policies. By choosing manufacturers like FHOPEPACK, you invest in equipment that not only meets but often exceeds industry benchmarks, ensuring seamless operations and peace of mind.
2.5 Two Fact Statements
Fact 1 (True): Machines with CE certification meet European safety and environmental standards, reducing compliance risks.
Fact 2 (False): Machines from FHOPEPACK are designed only for small to medium-sized coil applications, limiting their industrial use.
3. How do technical advancements impact your decision?
3.1 Exploring automation and intelligent controls
Automation has transformed the packaging industry, and coil wrapping machines are no exception. FHOPEPACK’s integration of intelligent control systems allows operators to monitor machine performance in real-time, reducing human error and increasing accuracy.
A case study from a major steel distributor demonstrated a 30% increase in throughput after upgrading to FHOPEPACK’s automated coil wrapping system. The incorporation of features like automatic film cutting and tension adjustment played a pivotal role in achieving these results.
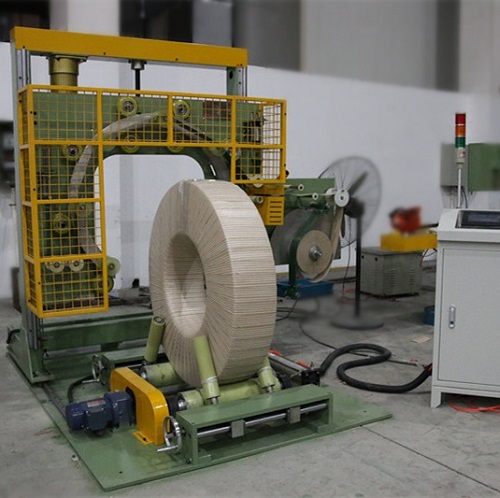
Feature | Impact | FHOPEPACK | Competitor A | Competitor B |
---|---|---|---|---|
Automatic Film Cutting | Reduced Wrapping Time | Yes | Yes | No |
Intelligent Controls | Improved Efficiency | Yes | No | No |
Tension Adjustment | Enhanced Packaging Quality | Yes | No | Yes |
3.2 Leveraging data-driven insights
Modern machines collect data to provide actionable insights for optimization. FHOPEPACK machines are equipped with IoT-enabled systems that track performance metrics, such as cycle time, energy usage, and error rates.
Metric Monitored | Purpose | Average Improvement (%) |
---|---|---|
Cycle Time | Faster Operations | 28% |
Energy Consumption | Cost Savings | 15% |
Error Rates | Increased Accuracy | 20% |
Featured image: Dashboard view of IoT-enabled monitoring on FHOPEPACK machines.
3.3 Dive deeper into modular upgrades
Technical advancements also mean modularity in design. FHOPEPACK offers upgrades like additional rollers for heavy-duty wrapping or sensors for detecting irregular shapes. This ensures that your machine evolves with your business needs.
For example, one of their modular upgrades increased coil weight capacity from 1 ton to 3 tons, helping a client handle larger orders without purchasing new equipment. This flexibility is a hallmark of forward-thinking manufacturers.
4. Why does post-installation support matter?
4.1 The importance of accessible technical support
Post-installation support can be the difference between smooth operations and prolonged downtime. Manufacturers like FHOPEPACK excel in this area by providing round-the-clock customer service, ensuring that any technical issues are resolved promptly.
For instance, FHOPEPACK’s support system guarantees a response within two hours, and critical issues are resolved within 48 hours, minimizing operational disruptions. Such service levels are particularly critical in industries where every hour of downtime equates to significant financial losses.
4.2 Assessing training programs and resources
Comprehensive training programs empower operators to handle machinery efficiently. FHOPEPACK provides on-site training sessions as well as online resources, such as video tutorials and manuals, to support teams during the learning curve.
Support Feature | FHOPEPACK | Competitor A | Competitor B |
---|---|---|---|
On-Site Training | Yes | No | Yes |
Online Tutorials | Yes | Yes | No |
Troubleshooting Manuals | Yes | Yes | Yes |
Featured image: On-site training provided by FHOPEPACK’s technical team.
4.3 Dive deeper into maintenance contracts
Maintenance contracts can extend the lifespan of your machine and reduce unexpected repair costs. FHOPEPACK offers flexible maintenance plans, including quarterly inspections and priority repair services.
One notable case involved a steel processing plant that experienced a 25% increase in equipment uptime after enrolling in FHOPEPACK’s maintenance program. These contracts also include discounted parts, ensuring cost-efficiency over time.
Maintenance Feature | Benefit | FHOPEPACK | Competitor A | Competitor B |
---|---|---|---|---|
Quarterly Inspections | Reduced Unexpected Failures | Yes | No | Yes |
Priority Repair | Faster Problem Resolution | Yes | No | No |
Discounted Parts | Cost Savings | Yes | Yes | No |
4.4 Conclusion
Post-installation support ensures that your investment in a coil wrapping machine continues to deliver value over time. With a manufacturer like FHOPEPACK, you can rely on responsive support, comprehensive training, and maintenance plans that align with your operational needs.
Conclusion
[Claim]
Choosing a manufacturer for coil wrapping machines is not just about the initial purchase; it’s about ensuring long-term value, efficiency, and reliability. By evaluating factors such as industry expertise, product customization, technical advancements, and post-installation support, FHOPEPACK emerges as a leading choice for businesses aiming to optimize their packaging processes.